12
2025
-
01
Анализ отказов и рациональное использование бурового инструмента
Рассмотрим меры по увеличению срока службы буровых долот, включая обоснованное определение конструктивных параметров наконечника, использование высококачественных материалов и передовых технологий производства.
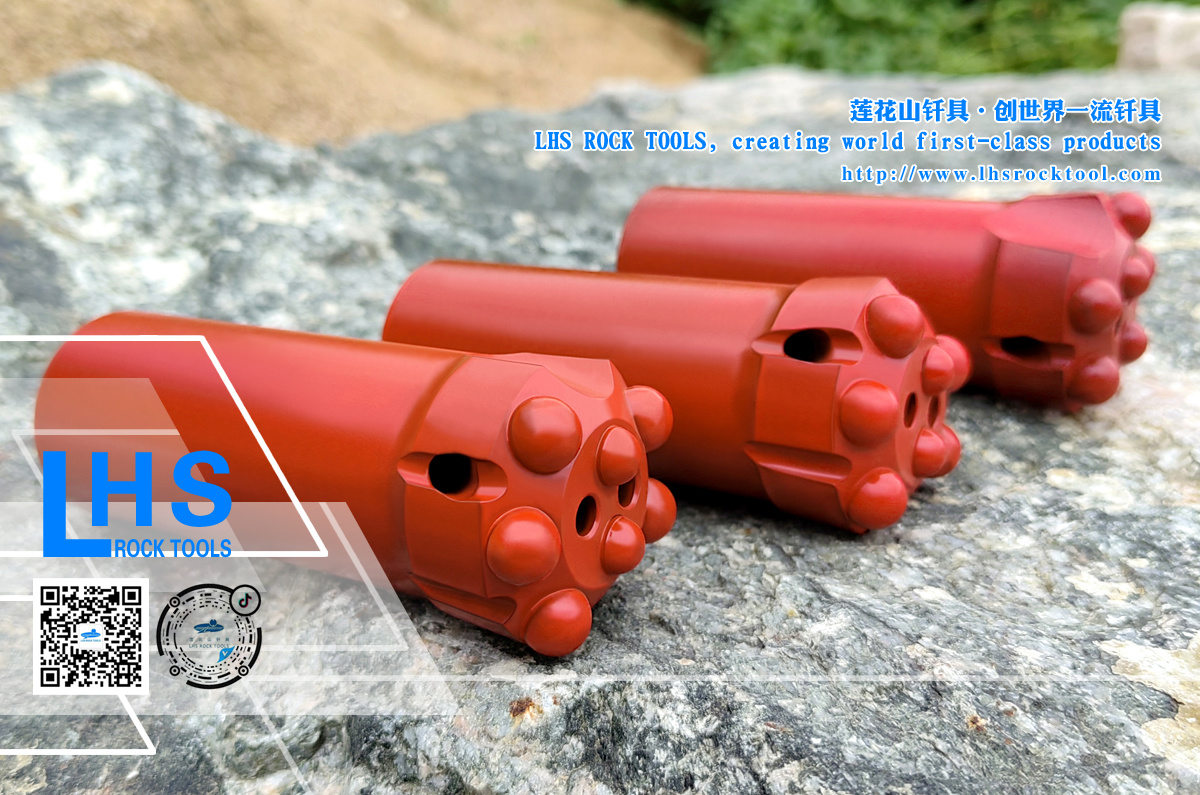
1 Анализ отказа бурового инструмента
В Китае уже создан ряд буровых инструментов с различными особенностями, таких как буровой инструмент с колончатыми зубьями, твердосплавные цельные буровые инструменты, буровой инструмент для очень твердых пород и т.д. Качество и срок службы постоянно повышаются, но их характеристики нестабильны. Основные причины преждевременного выхода из строя инструмента следует анализировать с точки зрения бурового долота и бурильной штанги. K610 Качество и срок службы постоянно повышаются, но их характеристики нестабильны. Основные причины преждевременного выхода из строя инструмента следует анализировать с точки зрения бурового долота и бурильной штанги.
Основные формы разрушения бурового долота включают фрагментацию, разрушение зубьев, выпадение зубьев, поломку и т.д., а также аномальный и нормальный износ. Основная причина выхода из строя долота типа "однозубое" заключается в том, что лезвия слишком тонкие, не износостойкие, быстро изнашиваются в радиальном направлении, геометрическая стабильность низкая, сила зажима лезвий недостаточна, что приводит к отслаиванию, некруглому отверстию, небольшому сопротивлению вращению и усиленному износу лезвий. Основные формы повреждения шарового долота включают выпадение краевых зубьев, разрушение зубьев, трещины, поломку и т.д. 7655 В Китайском геологическом университете с помощью ∅ 40、 ∅ 42 статистические данные по выходу из строя отечественных колончатых буровых долот при бурении твердого гранита показали : Выпадение краевых зубьев составляет 22,7% Разрушение краевых зубьев составляет 35,4% Выпадение и разрушение зубьев составляет 26,4% Полевые испытания показали : Выпадение и разрушение краевых зубьев являются наиболее распространенными формами повреждения. Это связано с тем, что краевые зубья подвергаются эксцентричному напряжению, которое распределяется крайне неравномерно, а также воздействию различных радиальных давлений на зубья, что приводит к неблагоприятным условиям нагружения краевых зубьев и их поломке. По мере увеличения ударной нагрузки на колончатое буровое долото пластическая деформация стенок зубчатых отверстий постоянно увеличивается, что приводит к появлению раструба в зубчатых отверстиях и снижению силы фиксации зубьев. Кроме того, слишком малый натяг в зубчатых отверстиях и низкая твердость корпуса бурового долота также усугубляют выпадение зубьев. Твердость корпуса бурового долота оказывает гораздо большее влияние на твердосплавные зубья, чем средняя и низкая твердость корпуса. Кроме того, это связано с такими факторами, как сварка, свойства флюса, сварочные работы и методы использования. 80% Разрушение корпуса бурового долота происходит в основном на границе между торцевой поверхностью хвостовика и основанием бурового долота, а частичное разрушение колончатого бурового долота происходит вдоль границы нижней части зубчатого отверстия. Кроме того, разрушение часто усугубляется из-за неправильного выбора марки стали, нерационального проектирования геометрических параметров, неподходящего выбора технологического процесса и неправильного использования.
В процессе работы бурильная штанга подвергается воздействию комбинированных переменных напряжений, в основном ударных, изгибных и коррозионных напряжений. Поэтому бурильная штанга должна обладать высокой усталостной прочностью, ударной вязкостью, коррозионной стойкостью, а также низкой чувствительностью к надрезам и скоростью распространения трещин. Формы разрушения бурильной штанги включают недостаточную твердость конца хвостовика малой бурильной штанги, что приводит к образованию наплыва : слишком высокая твердость приводит к разрушению; износ резьбы соединительной муфты, а также усталостный и хрупкий излом. Излом бурильной штанги является основной формой отказа. При многократном воздействии переменных напряжений в результате накопления повреждений образуются трещины, которые обычно возникают в слабых местах материала, таких как неметаллические включения, поры, белые точки, царапины, обезуглероживание, коррозионные трещины : Причины, связанные с качеством материала и термической обработкой, такие как чрезмерная твердость сердцевины цементированного стержня, плохая закалка, образование трещин и закалочных трещин на конце хвостовика, образование трещин и повреждений из-за конструктивных особенностей и плохого соединения хвостовика; неправильное использование, такое как следы от ударов молотком, плохая смазка соединительных узлов и коррозия бурильной стали, вызывающие трещины и разрушение. В процессе горных работ небольшая часть изломов бурильных штанг не имеет следов усталости, обычно они имеют блестящую кристаллическую структуру, что называется хрупким изломом. Это в основном связано с наличием дефектов в определенном месте бурильной штанги, таких как включения, вмятины, следы от ударов молотком или резкое изменение сечения, а также раструб, образовавшийся при ковке, неправильная термическая обработка и т.д., что приводит к низкой прочности бурильной штанги, плохой пластичности или образованию значительной концентрации напряжений, что приводит к очень быстрому развитию трещин и преждевременному хрупкому разрушению бурильной штанги.
2 Правильное и рациональное использование бурового инструмента
2.1 Повышение качества проектирования
Определение рациональных конструктивных параметров и постоянное развитие новых видов продукции являются предпосылками повышения срока службы инструмента. Форма зубьев колончатых буровых долот в большинстве случаев представляет собой полусферу, скорость бурения высокая, при вдавливании в породу поверхность зубьев испытывает значительное сжимающее напряжение, что обеспечивает прочность и долговечность. Размер зубьев должен обеспечивать достаточную прочность на растяжение и прочность фиксации зубьев. Анализ отказов показал, что краевые зубья находятся в неблагоприятных условиях нагружения, а выпадение и разрушение краевых зубьев являются основными формами повреждения бурового долота. Для уменьшения повреждения краевых зубьев и увеличения срока службы колончатых буровых долот можно принять следующие меры : ① Усиление краевых зубьев, правильный выбор формы, диаметра и высоты выступающих зубьев; ② Уменьшение угла наклона краевых зубьев способствует улучшению условий нагружения и повышению ударной прочности краевых зубьев; ③ Правильный выбор зазора между сварными швами и натяга фиксации зубьев для увеличения силы фиксации зубьев; ④ Использование для краевых зубьев твердого сплава с высокой вязкостью, прошедшего термическую обработку, эффективно предотвращает разрушение зубьев. Усиление корпуса бурового долота, повышение износостойкости корпуса; ⑤ Рациональное расположение зубьев, увеличение количества краевых зубьев по возможности, совершенствование системы удаления шлама, сохранение передних водяных отверстий и системы удаления шлама с большим зазором и тремя канавками и двумя отверстиями, высокая эффективность удаления шлама, уменьшение повторного дробления шлама, снижение энергопотребления и увеличение срока службы бурового долота.
Усовершенствование конструкции бурильных штанг, например, компания Ingersoll-Rand предложила бурильные штанги с полной резьбой, обработанные методом накатки, с поверхностной закалкой, что повышает вязкость и износостойкость, большой угол спирали, хорошую самоблокировку, удобство сборки и разборки. Повышение качества внешнего вида и упаковки инструмента, правильный дизайн формы и конструкции упаковки может эффективно защитить инструмент, улучшить его внешний вид и продлить срок службы.
2.2 Выбор высококачественных материалов
При выборе материала инструмента необходимо учитывать его прочность, износостойкость, хорошую жесткость и износостойкость, достаточно высокую усталостную прочность, низкую чувствительность к усталостным надрезам, высокую способность удерживать твердосплавные пластины и определенную коррозионную стойкость. : ① 24SiMnNi2 CrMo сталь является копией шведской стали FF710 Новая марка стали с наилучшими комплексными показателями механических свойств и сопротивления разрушению; ② 40SiMnMoV Средний накопленный проход бурового стержня, изготовленного из стали 1225.4m близок к зарубежному уровню; ③ 55SiMnMo Срок службы малых буровых стержней приблизился к шведскому 95CrMo малые буровые стержни 250m уровню; ④ 35SiMnMoV средний срок службы буровых стержней может достигать 300m/ штук. Указанные стали после закалки, отпуска, отжига и нормализации образуют бейнитную сталь с высокой прочностью при усталости и вязкостью. Для индукционной пайки пластин и зубьев малых буровых головок используется 40MnMoV в качестве материала корпуса буровой головки; для горячей запрессовки зубьев буровой головки используется 45NiCrMoV сталь. Выбор твердосплавного материала должен соответствовать механическим свойствам горных пород и типу буровой машины.
2.3 следует применять передовые технологии производства
Применение метода резания для производства буровых головок, позволяющего полностью заменить традиционную ковку механической обработкой, является новым достижением в технологии производства бурового инструмента. Паяние пластинчатых буровых головок должно осуществляться с использованием качественного нагревательного оборудования, такого как ультразвуковая или среднечастотная индукционная печь, которая позволяет осуществлять общий индукционный нагрев, предотвращая окисление и обезуглероживание заготовки, легко контролировать температуру, сокращать время нагрева и упрощать пайку. Необходимо строго контролировать воздушное или естественное охлаждение, чтобы предотвратить возникновение сварочных напряжений. Следует увеличить размер сварного шва, подобрать абразивные круги, тщательно очистить поверхность стали корпуса буровой головки и твердосплавных пластин органическими растворителями, такими как бензин, для повышения качества пайки.
Для зубчатых буровых головок большого и среднего диаметра рекомендуется использовать технологию горячей запрессовки зубьев, которая оказывает минимальное влияние на свойства корпуса буровой головки и твердого сплава, не повреждает поверхность зубьев и отверстий, обеспечивает стабильное качество, создает двухосное напряженное состояние на поверхности соединения зубьев и отверстий после сборки, улучшает качество запрессовки, уменьшает количество выкрашивающихся зубьев, позволяет реализовать оптимальный режим термообработки стали, полностью раскрыть потенциал стали и обеспечивает хороший внешний вид без протекания припоя.
Холодная запрессовка зубьев требует высокой точности обработки отверстий, поэтому часто используются высокоточные обрабатывающие станки, а конструкция оснастки предусматривает минимальную длину размерной цепи, что повышает жесткость контакта и качество поверхности зубьев и отверстий. При проектировании инструмента выбираются геометрические параметры резания с увеличенным пластическим деформированием и конструкция инструмента для упрочнения поверхности методом выдавливания, а сильная обработка резанием позволяет создать на поверхности стенок отверстий остаточные сжимающие напряжения и упрочненный слой в результате наклепа.
Для увеличения срока службы буровых стержней необходимо изготавливать точные пресс-формы для обработки, предотвращая образование раструба, облоя и трещин при ковке. Необходимо повысить качество прокатки полых сталей, устраняя или уменьшая вмятины, раковины, складки, обезуглероживание и другие поверхностные дефекты.
3 Заключение
В данной статье на основе анализа отказов бурового инструмента и исследования различных конструкций буровых головок и соответствующих видов разрушений обоснованы формы и причины отказов бурового инструмента, а также изложены меры по увеличению срока службы бурового инструмента с точки зрения определения рациональных конструктивных параметров, выбора высококачественных материалов и применения передовых технологий производства. Однако срок службы инструмента определяется его собственным качеством и правильной эксплуатацией, поэтому следует обратить внимание на следующие аспекты : ① При демонтаже буровой головки следует избегать ударов молотком, использование съемника буровых головок способствует увеличению срока службы инструмента; ② Заточка буровой головки способствует уменьшению образования и распространения поверхностных трещин и повышению скорости бурения; ③ Правильная эксплуатация, например, при бурении отверстий следует медленно продвигаться вперед, а после того, как буровая головка войдет в горную породу, работать на полной скорости, при соединении стержней следует обеспечить соосность трубы и хвостовика бурового стержня, а резьбу затянуть до упора; при заклинивании не следует бить по инструменту, а следует уменьшить подачу воздуха, увеличить подачу воды и медленно продвигаться вперед, постоянно совершая возвратно-поступательные движения, чтобы сделать стенки отверстия гладкими, а инструмент свободно перемещался, предотвращая таким образом разрушение твердосплавных пластин, поломку хвостовика и стержня, а также устраняя заклинивание.
В заключение следует отметить, что при любых условиях использование соответствующих буровых установок, специального бурового инструмента и соответствующего оборудования обязательно позволит раскрыть их потенциал.
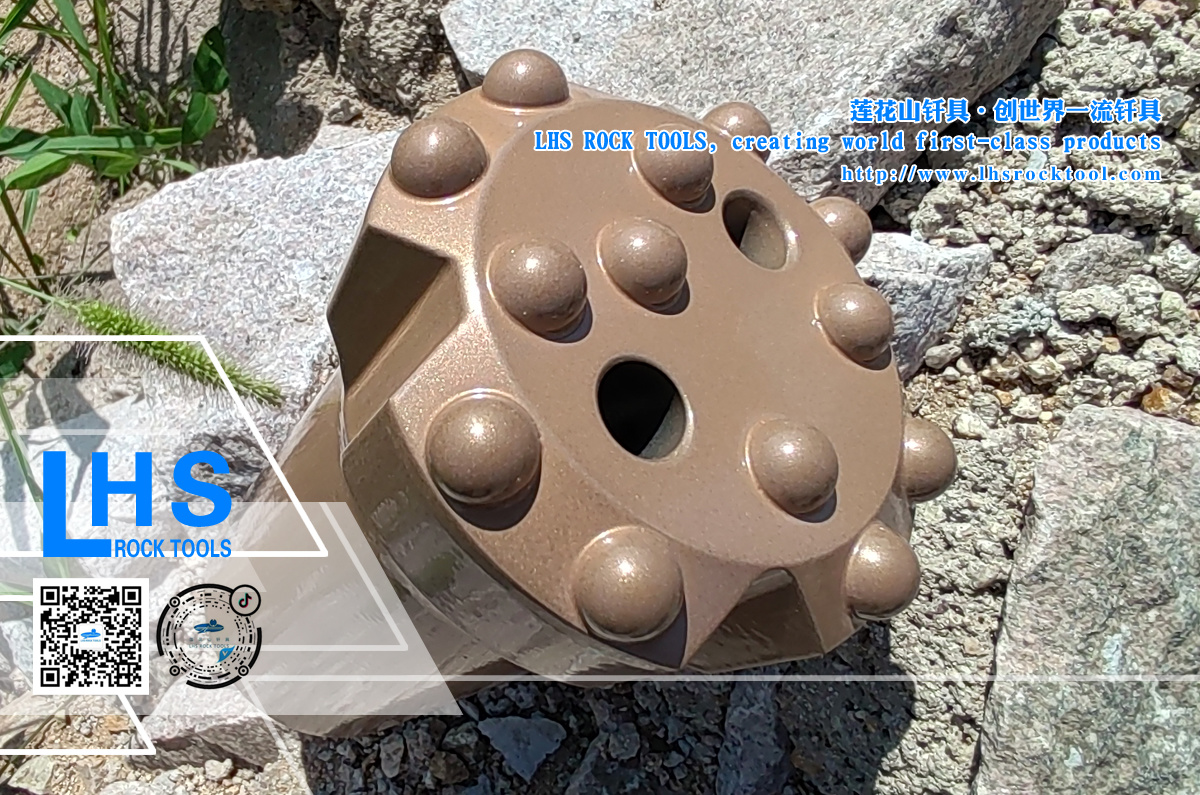
Предыдущая статья
следующая статья
Предыдущая статья
следующая статья
Связанная информация